ohbythebay
New member
- Thread Author
- #1
I think its a given that the best possible solution for cleaning records is the wet clean, vacuum type. Machines such as the VPI, etc. which range from approx. $400 to the $1000's. I like my vinyl clean. It reduces noise and wear. I also like convienance. My first was a spin clean but that required cleaning a bunch at once and putting away. Plus, no vacuum so in many ways I felt gunk was just driven into the grooves.
So seeing many threads, I built my own. Special note. You can build smaller. Mine is a little oversized. Generally, size is dictated by the size of the small shop vac you use and drive motor's ability to fit in a space. If I rebuilt, I could do it in half the size with a smaller vacuum I have. With that said...
Parts needed
Okay, the Basics.
You want to measure out first a top that will hold a platter and the arm wand. That is not so tough.
Then measure a box that will hold the vacuum and motor underneath. This is an important step because you have to measure a height GREATER than the Vacuum that includes the motor. Why? Because unless you make the box wide (like mine) motor underneath and the vacuum cannot occupay the same space. So if the vacuum is 12" and motor is 4", give your self at least a 20" box or it will get REAL TIGHT. Something like this:
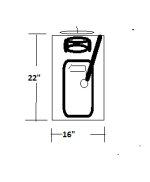
So you now have it mapped out, where the platter will go, how it will all fit (don't do the VPI wand hole yet, that comes later.
Dont let this part scare you - its the toughest but just think it through.
The toughest part of this whole thing is the spindle to motor. Most motors like this have a square hole for a shaft. Many bolts have a square head, some a hex. The idea is to get a bolt that will fit in the motor, up through the wood and fit through the platter (7mm bolt). You will be mounting the motor to the underside of the top board so that it spins freely but is TIGHT and STRAIGHT in the hole. Any angle on the shaft will create a wobble in the platter. so you want to keep that UNDERSIDE distance as short as possible.
Now this is where your own head needs to come in because the object is to mount in the motor, have washers on both sides of the board and CONNECT that bolt to the platter so that when the shaft turns, the platter turns. If its not connected it will just turn in place and not turn the platter. So how do you do this...? See diagram
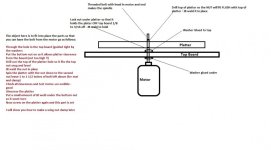
So seeing many threads, I built my own. Special note. You can build smaller. Mine is a little oversized. Generally, size is dictated by the size of the small shop vac you use and drive motor's ability to fit in a space. If I rebuilt, I could do it in half the size with a smaller vacuum I have. With that said...
Parts needed
- Wood for a cabinet (I used MDF) or a small put together end table that you would get from say target or wall mart like this - http://www.walmart.com/ip/Sauder-End-Table-Milled-Cherry/21094262?_mm=
- A Platter from an old TT
- An AC powered motor from an ice cream machine or barbecue rotisseree (more on this)
- A shop vac (small) AC powered - not the little DC ones for cars, not enough suction
- An onn/off switch or toggle
- Some threaded bolts for a shaft along with some washers
- A wing nut and rubber washers
- A VPI Wand kit (biggest expense - about $70) - http://www.elusivedisc.com/VPI-HW-16-TO-HW-165-UPGRADE-KIT-NO-DUST-COVER/productinfo/HW-3015/
- A Tube of JB Weld
Okay, the Basics.
You want to measure out first a top that will hold a platter and the arm wand. That is not so tough.
Then measure a box that will hold the vacuum and motor underneath. This is an important step because you have to measure a height GREATER than the Vacuum that includes the motor. Why? Because unless you make the box wide (like mine) motor underneath and the vacuum cannot occupay the same space. So if the vacuum is 12" and motor is 4", give your self at least a 20" box or it will get REAL TIGHT. Something like this:
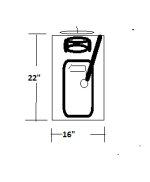
So you now have it mapped out, where the platter will go, how it will all fit (don't do the VPI wand hole yet, that comes later.
Dont let this part scare you - its the toughest but just think it through.
The toughest part of this whole thing is the spindle to motor. Most motors like this have a square hole for a shaft. Many bolts have a square head, some a hex. The idea is to get a bolt that will fit in the motor, up through the wood and fit through the platter (7mm bolt). You will be mounting the motor to the underside of the top board so that it spins freely but is TIGHT and STRAIGHT in the hole. Any angle on the shaft will create a wobble in the platter. so you want to keep that UNDERSIDE distance as short as possible.
Now this is where your own head needs to come in because the object is to mount in the motor, have washers on both sides of the board and CONNECT that bolt to the platter so that when the shaft turns, the platter turns. If its not connected it will just turn in place and not turn the platter. So how do you do this...? See diagram
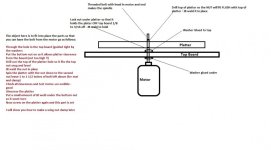